States of Lubrication: Hydrodynamic, Boundary, Mixed Film
Motor Oil’s primarily role is to lubricate the engine. Once an engine is started, the oil must circulate promptly and lubricate all moving parts to prevent the metal to-metal contact that would result in wear, scoring, or seizure of the engine.
Friction is the force that resists relative motion between two bodies in contact. If friction didn’t exist, nothing would ever stop moving. We need friction to function, but there are instances where you want to be able to reduce the amount of friction present.
A reduction in friction leads to less wear on components, easier movement, and reduced energy needs of the system. In fact, some well-designed engine oils can actually increase a car’s fuel economy.
Friction generates heat, so for a lubricant to be successful, it needs to retain its lubricity (slipperiness) even when it gets hot. If a lubricant lacks thermal stability, then it begins to break down when it gets hot, which leads to increased friction.
Motor Oils must lubricate and prevent wear in all temperature extremes. Oil that does not flow well in cold temperatures will leave parts of the engine with no protection at start-up (this is when the most metal to metal contact occurs and thus the most wear).
On the other hand, oil that becomes too fluid at high operating temperatures will not be able to maintain an adequate film thickness between moving parts.
Oil flow also refreshes critical additives to the working surfaces. This reserve additive supply includes anti-wear additives, friction modifiers, corrosion inhibitors and others. Lubricant starvation produces elevated heat, which rapidly depletes additives.
There are 3 States (or Regimes) of Lubrication:
1- Hydrodynamic/Elastohydrodynamic Lubrication (Full Film)
2- Boundary Lubrication
3- Mixed Film Lubrication
1- Hydrodynamic/Elastohydrodynamic Lubrication
The goal of motor oil is to provide and maintain a “full” lubrication film between moving parts. Under full-film lubrication conditions, a thick film of oil prevents metal-to-metal contact between moving engine parts; the load is fully supported by the lubricant.
Even on the most polished and smooth surfaces, irregularities are present. They stick out of the surface forming peaks and valleys at a microscopic level. These peaks are called asperities. In order for full-film conditions to be met, the lubricating film must be thicker than the length/height of the asperities.
Full-film lubrication occurs when the moving surfaces are continuously separated by a film of oil. Under ideal conditions, this type of lubrication will not allow wear. Crankshaft bearings, as well as connecting rods, cam-shafts and piston rings, normally operate with full-film lubrication.
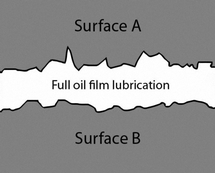
There are two types of “Full-Film” lubrication, Hydrodynamic and Elastohydrodynamic.
Hydrodynamic Lubrication (HL) occurs when two surfaces in sliding motion (relative to each other) are fully separated by a thick film of oil.
The most common example would be a journal bearing where the motion of the contacting surfaces and the exact design of the bearing are used to pump lubricant around the bearing to maintain the lubricating film.
When a shaft is still, it sits on the bottom of the bearing, but when it starts to move, it tries to “climb” up the side of the bearing. Microscopic layer upon layer of the lubricant create friction with each other and form an oil wedge between the shaft and the bearing, protecting both surfaces.
Elastohydrodynamic Lubrication (EHL) is similar but occurs when the surfaces are in a rolling motion (relative to each other). The film layer in elastohydrodynamic conditions is much thinner than that of hydrodynamic lubrication, and the pressure on the film is greater. It is called elastohydrodynamic because the film elastically deforms the rolling surface to lubricate it.
Elastohydrodynamic lubrication is mostly for nonconforming surfaces or higher load conditions where the bodies suffer elastic strains at the contact. Such strain creates a load-bearing area, which provides an almost parallel gap for the fluid to flow through.
Much as in hydrodynamic lubrication, the motion of the contacting bodies generates a flow induced pressure which acts as the bearing force over the contact area. In such high pressure regimes, the viscosity of the fluid may rise considerably.
Elastohydrodynamic Lubrication is present in rolling contacts, such as ball bearings or roller bearings. In this situation, the softer material makes up the rolling element which actually deforms for a split second to enlarge the contact area between mating surfaces. Here, the oil film thickness is one micron or less. At full Elastohydrodynamic lubrication the generated lubricant film completely separates the surfaces.
The determining factor in keeping these parts separated is the viscosity (thickness) of the oil at its operating temperature. The viscosity of the oil should be high enough to maintain an unbroken film and prevent metal-to-metal contact, but should not be higher than necessary since this increases the amount of force required to overcome this fluid friction.
Since the metals do not make contact in full-film lubrication, wear is negligible – unless the separated parts are scratched by particles thicker than the oil film itself.
2- Boundary Lubrication
Under certain conditions, it is impossible to maintain a continuous oil film between moving parts and there is intermittent metal-to-metal contact between the high spots (asperities) on sliding surfaces.
Under these circumstances, the load is only partially supported by the oil film. The oil film is squeezed-out or ruptured which can result in significant metal-to-metal contact. When this occurs, the friction generated between the surfaces can produce enough heat to cause one or both of the metals in contact to melt and weld together.
Unless counteracted by proper additive treatment, the result is either immediate seizure or the tearing apart (shearing) and roughening of the surfaces.
Lubrication specialists call this Boundary Lubrication.
Additives, such as anti-wear (AW) agents and extreme-pressure (EP) agents, help protect surfaces and can greatly reduce the amount of damage that can occur during boundary lubrication.
At elevated temperatures and pressures these additives chemically react with the contact surface forming a highly resistant tenacious film (sacrificial layer) on the moving surfaces which is capable of supporting the load and major wear or breakdown is avoided.
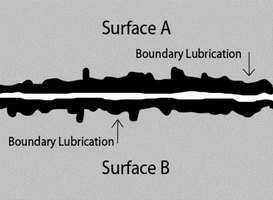
Boundary lubrication occurs when the two surfaces are contacting in such a way that only the EP or AW layer is all that is protecting them. These additives are the last line of defense for a lubricant to protect your equipment. This is not ideal, as it causes high friction, heat and other undesirable effects.
Boundary lubrication conditions always exist during engine start-up, until the oil gets to the bearings and valve train, and where shock-loading conditions are present.
Boundary lubrication is also found around the top piston ring where oil supply is limited, temperatures are high, and the oil is displaced, cleaned by the oil control rings.
3- Mixed Film Lubrication
Mixed Film Lubrication, as the name implies, is a cross between boundary and hydrodynamic lubrication.
Mixed Film Lubrication is where lubrication is marginal. While the bulk of the surfaces are separated by a lubricating layer, the asperities still make contact with each other. This is where the additives again come into play.
Under high-load conditions oil is squeezed under pressure. For example, during acceleration of an engine, you step on the gas and the engine dumps fuel, in turn the force is increased against the rod bearings, pushing (or squeezing) on the hydrodynamic oil creating a marginal lubrication condition.